Success in business, like success in athletics, is often tied to the ability to be faster and more agile than an opponent. Success in scientific research tends to be achieved through a slower, nuanced process that’s judged by the accuracy of the data collected.
But for Leslie Lamberson, PhD, an assistant engineering professor whose lab examines how things break when they’re hit – “successful” science is all about speed.
And for Jing Liang and Claudio Storelli, founders of an upstart company that’s breaking into the protective athletics wear market, scientific testing is key to making their products hold up against wear and tear of competition and for their business to edge out more established brands in a growing area of the market.
The unwitting contemporaries found each other last fall when a student project brought Storelli’s materials to Lamberson’s lab — the impact of the collaboration changed the course of both sets of visionaries.
In the Field
Storelli, the company, was founded by Storelli and Liang in 2011 after years of playing through nagging injuries suffered in rec soccer games led them to the realization that they could eliminate some bumps and bruises by working a bit more padding into their soccer kits.
“We played together in the New York soccer leagues and used to find ourselves getting pretty dinged up during our soccer matches. Anyone who’s played the sport knows, that nagging injuries can really slow you down — and we’re not talking about major injuries, just the bumps, bruises and turf burns that happen all the time,” Liang said. “Claudio and I realized that there really wasn’t much out there to protect athletes from these injuries so we started developing lightweight and impact resistant gear to protect knees and elbows and shins so you can play your game, fearless. It just went from there.”
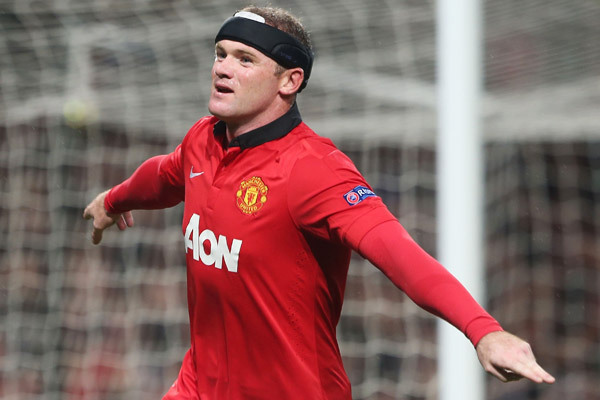
Since then Storelli has expanded into protection for just about any body part that gets beat up during competition, heads and shoulders to knees and elbows.
The company got a big break in 2013 when the pair acted quickly to ship some of its protective headbands to English soccer star Wayne Rooney, when he suffered a head laceration. Using the band, Rooney, whose injury had kept him off the field for more than a month, returned to action sporting the Storelli headgear, to lead his Manchester United team to victory.
While the exposure helped put Storelli’s brand on the map, the company, whose mission is to change the world of soccer, is constantly pushing forward to improve its products. With product already widely worn by players at all levels, Storelli signed its first two professional soccer players as brand ambassadors earlier this year and, according to Liang, hopes to take the soccer world by storm soon.
In the Lab
Like Liang and Storelli, Lamberson has built her operation from the ground up. Or, more precisely, from the impact testing devices she uses to break things, to the reinforced walls that prevent them from breaking things they’re not supposed to.
The centerpiece of Lamberson’s Dynamic Multifunctional Materials Lab is a 12-foot, two-stage light-gas gun that can propel a projectile 7,000 miles per hour into a test material while imaging technology captures the impact frame by frame.
Lamberson’s patented two-stage, light-gas gun allows her lab to conduct a range of material testing research.
NASA uses one, built from a modified 44-mm cannon as a cost estimated in the millions, to understand what micrometeorites do to the outside of rockets and space shuttles. Lamberson designed and built hers on a $30,000 budget with parts acquired from Ikea and an industrial supply catalogue.
To study a material’s behavior under hypervelocity impacts like this, you either own a tool like this or you have to send your material to a lab, pay thousands of dollars per test and wait weeks for the results.
“I knew what capability I needed to conduct my research, but creating facilities at the scale of NASA just isn’t feasible in academia, so I had to figure out a way to make it work,” Lamberson said. “Most of the high-end testing equipment in specialized facilities can be reverse engineered, optimized for smaller-scale research, and redesigned with parts that are reasonably priced and readily available, so that’s what we did.”
In addition to the big gun, Lamberson’s lab has a number of other tools she’s assembled —and patented — to poke, push and pull materials to their limits.
On a lab bench next to the light gas gun, is a piston-like contraption that serves a similar purpose but on a smaller scale. Lamberson also designed and built this novel testing tool, called a dynamic fatigue impact testing device. If the light gas gun performs the equivalent of testing a material’s strength by shooting a bullet at it, then this device performs a task you’d liken to testing durability by repeatedly poking it.
Lamberson uses the impact or dynamic fatigue device (or DFD for short) to study everything from bone breaks to military body armor. But an interesting new opportunity came her way when a group of senior design students decided they wanted to study protective headgear used by soccer players.
Contact
Students in Lamberson’s lab broached a relationship with Storelli when they were searching for samples of athletics headgear to test.
Intrigued by the prospect of replicating repeated impacts on their materials would experience on the field, the company sent Lamberson’s lab a sample of its protective headgear and some of the other materials they were considering using in future models.
When the first round of results came in, Jing and Storelli realized the quality of the data they were getting from the research team. The decided to sponsor the students’ project, provided that they build them a tabletop version of the dynamic fatigue device they were using to perform the testing.
The company’s main obstacle, like Lamberson’s initial hurdle, was a scarcity of quality testing equipment for this type of loading.
“We test a lot of shock absorbing materials — the one’s we’re currently using, new ones that we’ve found, ones that we’re thinking about using in the future — so we’re constantly looking for ways to evaluate the materials and rank their order of performance against each other,” Liang said.
In the design of the new device, the team decreased its overall size to make it more portable, while increasing the size of the projectile – to more accurately represent impact scenarios the gear would take during use. They also used a more powerful actuator and motor to push the projectile into the material, because of its relative thickness. And they made a version of the impact zone that is rounded, to replicate the shape of a head and fit the headgear, and added a force-measuring device located where the middle of the forehead would be to take readings.
Lamberson and the students delivered Storelli’s device in the fall, and trained Liang and the company’s in-house research and development team on using it.
“The design is a lot more sleek and specialized for this particular type of testing,” Lamberson said. “The goal was to make it as user-friendly as possible, from mounting the test material, to creating a true-to-life impact, to delivering data that doesn’t require additional interpretation to understand.”
The tabletop tester can give nearly immediate feedback on how the material receives and disburses the force of the impact, also known as the force spike. It shows how long the impact is felt, how quickly it disburses and how rapidly it passes through the material from front to back — all important metrics when selecting a pad material and a configuration to minimize the amount of force that is felt by the person wearing the gear. What’s more, the tester can do this for up to millions of impacts, so Storelli can determine not only how the headgear performs out of the box, but also how it holds up during a normal lifespan of use.
“This is a really helpful tool because in the past what we did was send out foam to outsource lab to do some testing procedure that takes a long time and is expensive and we don’t see the data for three weeks,” Laing said. “This lets us test and get results almost in real-time. It eliminates 80 percent of our guesswork, which speeds our process of design and redesign.”
According to Liang, the company’s research and development team is now using the device many times each week to evaluate new foams and shock absorbing materials. Though the device was originally designed with headgear testing in mind, it is also effective for testing pad configurations on Storelli’s other products including knee, elbow and hip pads, shin guards and protective shorts.
“It’s an integral part of our R&D strategy,” Liang said. “There aren’t any off-the-shelf machines on the market that can test impact — and that’s what we’re trying to do here: test the basic principles of shock absorption materials. Now we have a machine that’s custom built for it.”
With her lab in full operation, Lamberson is continuing to push forward with her research as well. Some of her most recent work will help to improve composite materials that keep ship hulls and airplane engines safe from punctures.