MXene-coated Devices Can Guide Microwaves in Space and Lighten Payloads

- Drexel’s College of Nursing and Health Professions Receives $1 Million for Scholarships from the Bedford Falls Foundation – DAF to Address Nursing Workforce Shortage
- U.S. Department of Education Provides Final Approval of Drexel and Salus Merger
- Spotting Bad Batteries Before They Malfunction
- When Climate Disasters Hit, They Often Leave Long-term Health Care Access Shortages, Drexel Study Finds
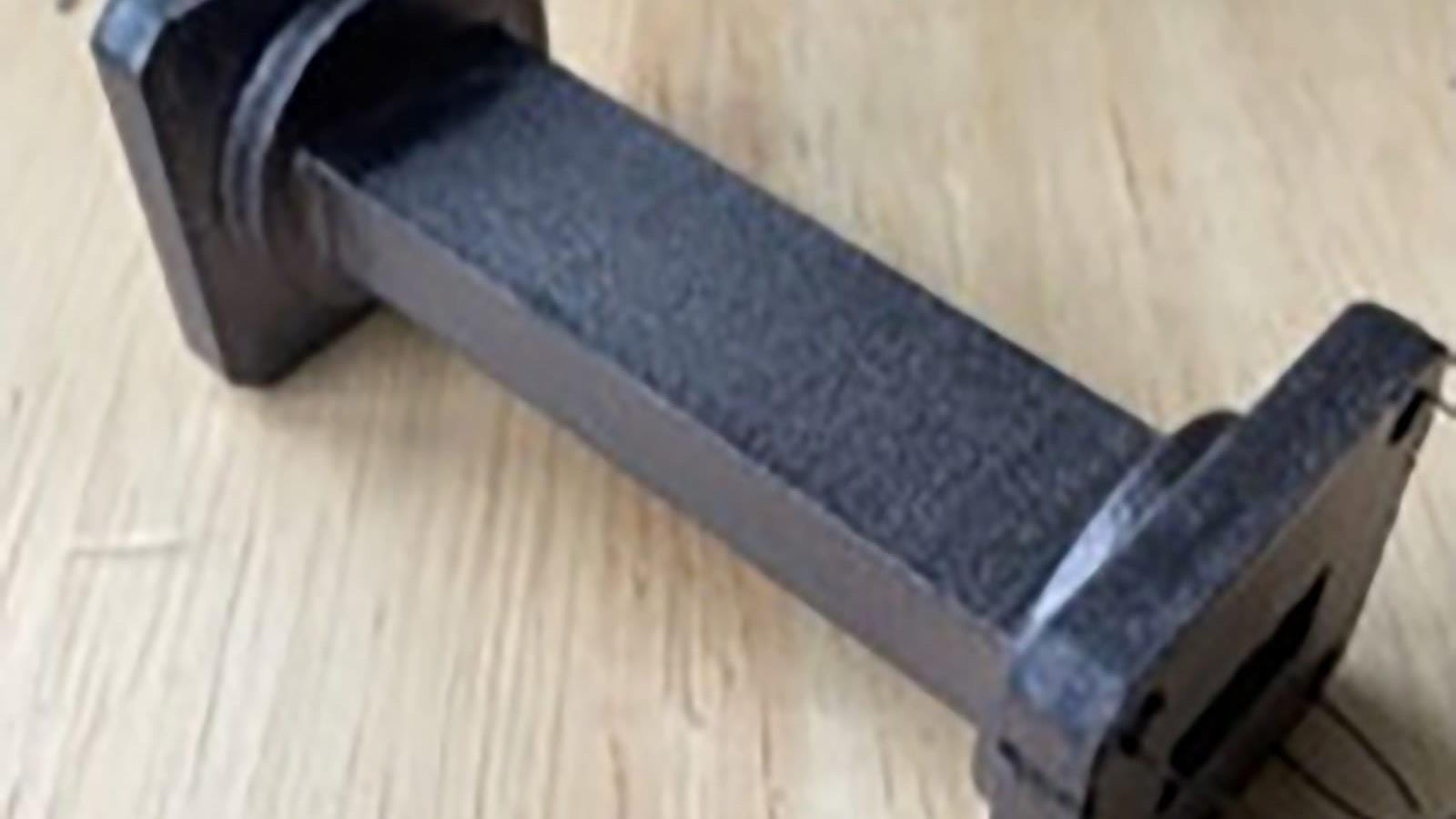
Waveguides are the pipes that direct and focus electromagnetic waves in telecommunications satellites and terrestrial devices like microwaves and phones.
One of the most important components of satellites that enable telecommunication is the waveguide, which is a metal tube for guiding radio waves. It is also one of the heaviest payloads satellites carry into orbit. As with all space technology, reducing weight means reducing the amount of expensive and greenhouse gas-producing fuel it takes to launch a rocket, or increasing the number of devices carried by the same rocket to space. Researchers from Drexel University and the University of British Columbia are trying to lighten the load by creating and testing a waveguide made from 3D-printed polymers coated with a conductive nanomaterial called MXene.
In their paper recently published in the journal Materials Today, the group reported on the potential of using MXene coatings to impart lightweight nonconductive components with electrical conductivity — a property sacrificed in additive manufacturing using polymer materials, such as plastics.
“In spaceflight applications, every extra gram of weight counts,” said Yury Gogotsi, PhD, Distinguished University and Bach Professor in Drexel’s College of Engineering, who is a leader in MXene research. “MXene materials provide one of the thinnest possible coatings — their flakes have a thickness of a few atoms — that can create a conductive surface, so we see great potential in using MXenes to treat additive manufactured components made of polymers that have complex shapes.”
Waveguides function as pipelines for microwaves. They direct the waves to receivers while preserving the power of the signal. In a microwave oven, waveguides ensure heating of the food; on a satellite, they transfer high-quality signals between different objects within and between satellites, as well as between satellites and Earth.
And, like the intricate network of pipes winding their way through a home, waveguides are designed in a range of shapes to fit into confined spaces. They can range from simple, straight channels to structures as complex as a labyrinth.
"Waveguides can be as basic as a straight, rectangular channel or they can morph into shapes resembling a 'crazy straw,' with bends and twists," said Mohammad Zarifi, an associate professor, who studies microwave communication at the University of British Columbia and led the team’s electrical engineering and design efforts. “The real game-changer, however, is the advent of additive manufacturing methods, which allow for more complex designs that can be difficult to produce with metals.”
While just about any hollow tube could be used as a primitive “waveguide,” the ones that transmit electromagnetic waves — in microwave ovens and telecommunications devices, for example — must be made from a conductive material to preserve the quality of transmission. These waveguides are typically made from metals like silver, brass and copper. In satellites, aluminum is the lighter-weight choice.
The researchers from Drexel, who first discovered MXenes in 2011 and have led their research and development ever since, suggested the 2D nanomaterials would be a good candidate as a coating for the plastic waveguide components based on their previous discoveries that MXenes can block and channel electromagnetic radiation.
“Our MXene coating emerged as a strong candidate for this application because it is highly conductive, functions as an electromagnetic shield and can be produced simply by dipping the waveguide in MXenes dispersed in water,” said Lingyi Bi, a PhD candidate in Gogotsi’s group. “Other metallic paints have been tested, but due to the chemicals used to stabilize their metallic ingredients, their conductivity suffers in comparison to MXenes.”
In addition, the researchers reported that the MXene coating bonded exceptionally well to the 3D-printed nylon waveguides due to compatibility between their chemical structures. The team dip-coated lightweight guides of varying shapes and sizes — straight, bent, twisted and resonator-shaped — to test MXene’s ability to thoroughly cover their interior.
The MXene-coated nylon waveguides weigh about eight times less than the standard aluminum ones currently being used, and the MXene coating added just a tenth of a gram to the overall weight of the components.
Most importantly, the MXene waveguides performed nearly as well as their aluminum counterparts, showing an 81% efficiency in guiding electromagnetic waves between two terminals after just one cycle of dip coating, just a 2.3% drop off from the performance of aluminum. The researchers demonstrated that they could improve this transmission metric by varying layers of coating or the size of MXene flakes — reaching a top transmission efficiency of 95%.
This performance held steady when the transmission was dialed up to the different frequency bands, such as those currently used in low-Earth orbit satellite communications and a sufficiently high input power for these transmissions. It also did not significantly degrade after three months, an indicator of the durability of the coating.
“The MXene-coated waveguides still need to go through extensive testing and be certified for space use before they can be used on satellites,” said Roman Rakhmanov, a doctoral candidate at Drexel who participated in the research. “But this finding could be an important step toward the next generation of space technology.”
Gogotsi’s team plans to continue its exploration of MXene coatings in applications that could benefit from an alternative to metal components.
“These promising results suggest that MXene-coated components could be a viable lightweight replacement for waveguides used in space,” Gogotsi said. “We believe that the coatings could also be optimized for transmissions of varying frequencies and applied to a variety of additive-manufactured or injection-molded polymer components, providing a lightweight and low-cost alternative to metals in a number of terrestrial applications as well.”
This research was supported by the U.S. National Science Foundation. In addition to Gogotsi, Rakhmanov and Bi, from Drexel; Omid Niksan, Kasra Khorsand Kazemi and Mohammad H. Zarifi, from the University of British Columbia, contributed to this research.
Read the full paper here: https://www.sciencedirect.com/science/article/pii/S1369702123004133
Drexel News is produced by
University Marketing and Communications.