Using Viruses To Help Water Blow Off Steam

- Spotting Bad Batteries Before They Malfunction
- When Climate Disasters Hit, They Often Leave Long-term Health Care Access Shortages, Drexel Study Finds
- New Research Highlights Health Benefits of Using Heritage Art Practices in Art Therapy
- Chief Defender at the Defender Association of Philadelphia, Keisha Hudson, Will Address Drexel Kline School of Law Graduates at Commencement
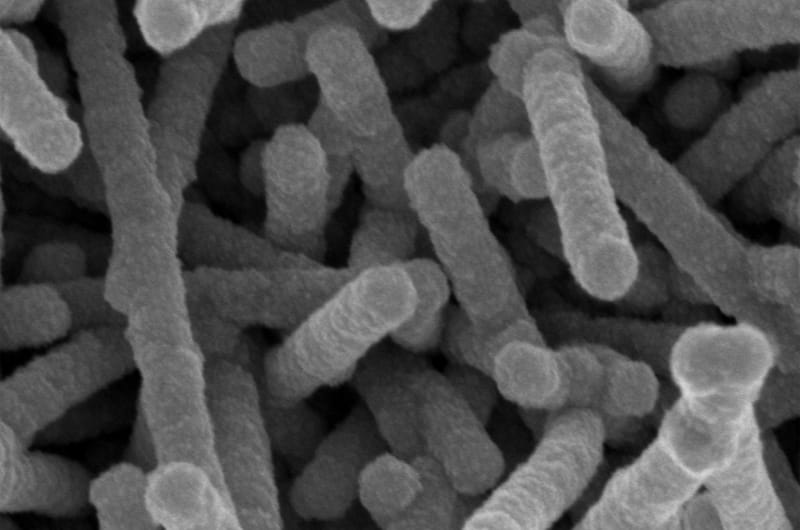
Tobacco mosaic viruses serve as the template for building nickel-coated nanostructures that enhance the boiling process.
Legions of viruses that infect the leaves of tobacco plants could be the key to making power plants safer, heating and cooling of buildings more efficient, and electronics more powerful. These tiny protein bundles, which were once a threat to a staple cash crop of the nascent United States in the 1800s, are now helping researchers like Drexel University’s Matthew McCarthy, PhD, better understand and enhance the processes of boiling and condensation.
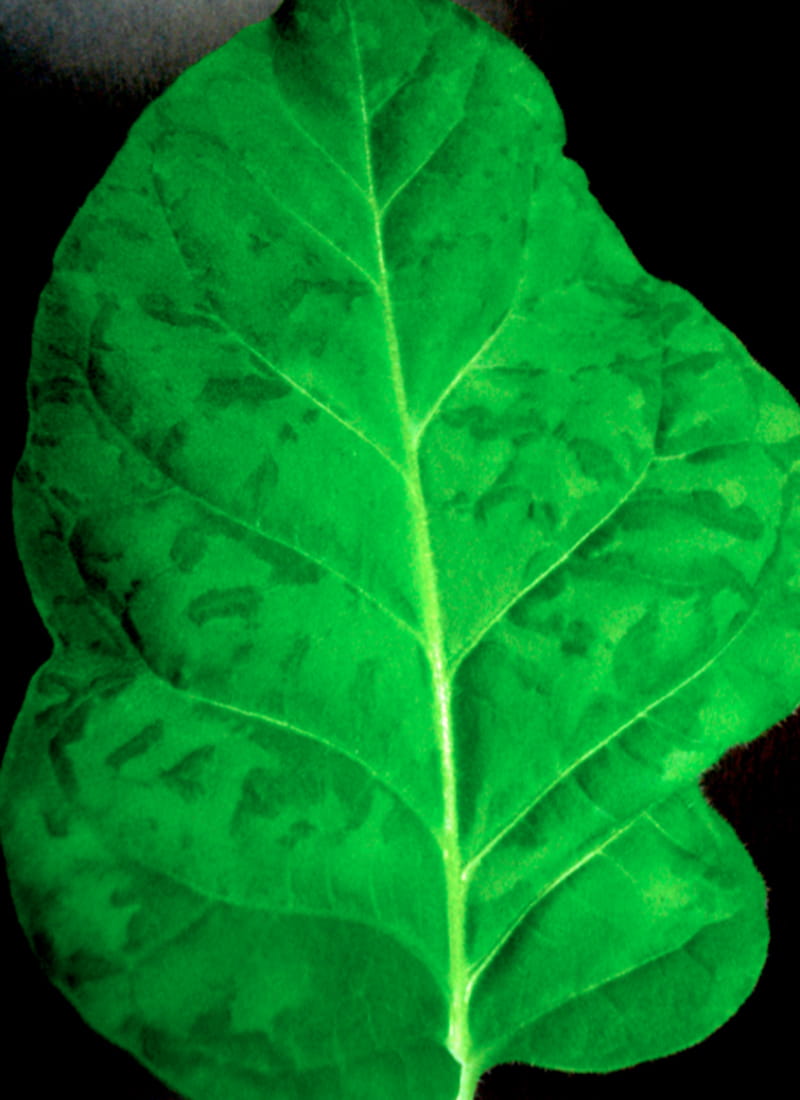
McCarthy’s research focuses on phase-change heat transfer—the boiling, evaporation and condensation of fluids. These processes, which are ubiquitous in nature, have also become integral to the technologies that keep our society running. Steam turbines generate electricity in massive plants that power cities. Boiling water is a time-tested purification method that is still used to treat water supplies. And both heating and cooling processes are part of the systems that control our indoor climates on a daily basis. If McCarthy’s work can make phase-change heat transfer even a little more efficient its impact could be huge.
“Even slight improvements to technologies that are used so widely can be quite impactful,” McCarthy said. “Phase-change heat transfer plays an important role in everything from power generation to water purification, HVAC and electronics cooling. Increasing performance of these systems would translate to significant improvements in the way we produce, consume and conserve our energy and water resources.”
Better Boiling?
To improve on something that nature has been doing since the beginning of time, and people have been refining for thousands of years, McCarthy’s looking not at the liquid or the heat source, but at the surface that links them.
In his Multiscale Thermofluidics Lab, McCarthy and his team design, build and test surfaces that are becoming increasingly better at controlling the formation and removal of vapor bubbles during the boiling process, while also delaying the onset of and undesirable condition that engineers call “critical heat flux.”
“Critical heat flux is essentially the failure of a surface during boiling, where the production of vapor cannot be balanced by replenishing liquid,” McCarthy said. “The result is an uncontrollable and often dangerous increase in surface temperature. This failure can lead to the simple destruction of electronic components, or in power plant cooling applications, the catastrophic meltdown of a nuclear reactor.”
When a liquid reaches critical heat flux a thin layer of vapor blankets the heat-transfer surface. This vapor insulates the liquid from the heat source and it drastically reduces the surface’s ability to dissipate heat to the liquid. This results in “burnout,” which means dangerous increases in surface temperature occur very rapidly. After critical heat flux and burnout occur, it is extremely difficult to re-wet the surface and reduce its temperature.
McCarthy’s goal is to create nanostructured coatings for the heat-transfer surfaces that can delay or prevent the vapor barrier from forming in the first place. The ideal structure for higher heat transfer during boiling, according to McCarthy, is one that draws in the liquid and quickly rewets when the water does transform into a vapor.
A “Dri-Fit” Boiling Surface
“The only way to delay CHF is to keep the surface wet at higher and higher heat fluxes.” McCarthy said.
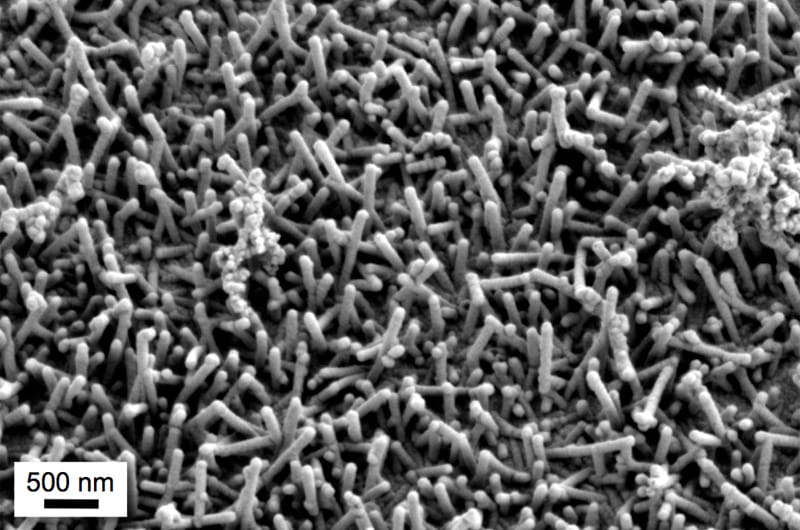
To keep the boiling surface wet, McCarthy’s team is employing a technique that’s more frequently used to keep athletes dry. Wicking, or capillary effect, is the secret behind the high performance and thermal apparel that draws moisture away from the body. This material, which keeps people cool during a workout or warm in the winter, can also keep a boiling surface wet—thus staving off critical heat flux.
The trick to making a wicking, or hydrophilic material, is strategically increasing its surface area to draw the liquid down a path toward region of lower density. Sponges do this with their pores and air pockets. McCarthy’s team is creating its own super-hydrophilic surfaces by coating them with thousands of nanostructure tendrils. This is where the viruses come in.
Viral Building Blocks
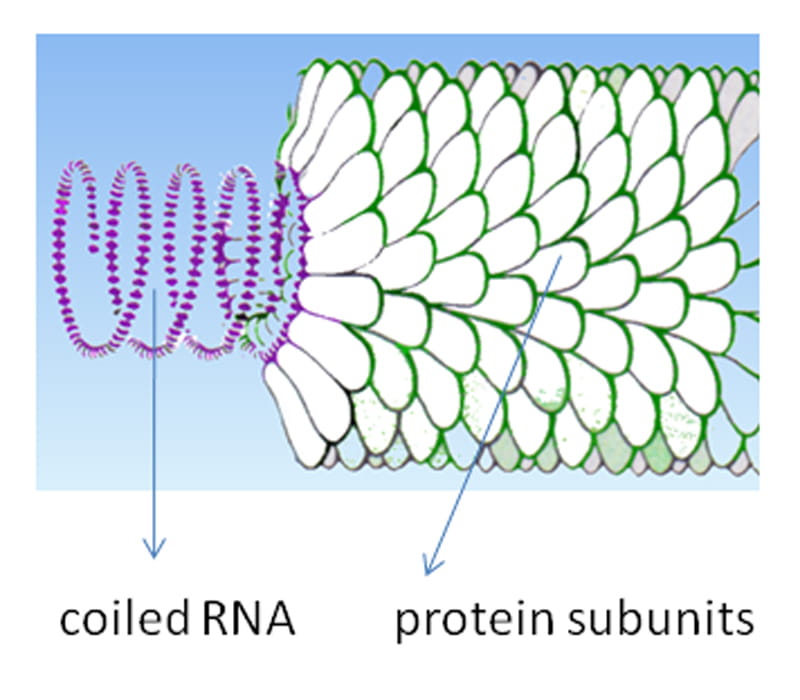
The Tobacco mosaic virus, is a simple virus consisting of a single strand of RNA surrounded by thousands of coat protein strands. It was the first virus ever to be identified, in 1930, and one of the most extensively studied—likely because they were destroying an important cash crop at the turn of the last century. Today the pests have carved out a new niche: self-assembling scaffolding for building nanostructures.
McCarthy has been directing minions of Tobacco mosaic viruses since he was a post-doctoral researcher at the University of Maryland, when his lab used them for research on nanostructured battery electrodes. He now grows his own genetically modified strain of the virus on the tobacco plants in his lab.
“The genetic mutation introduces chemical binding sites—like molecular hooks—on the outer surface of the viruses that allow them to attach to nearly any substrate we want to use,” McCarthy said. “This includes stainless steel, aluminum, copper, gold, silicon, and a variety of different polymers. Because of this we are able to do a rather broad array of testing on materials that are already in use in power plants and water treatment facilities today.”
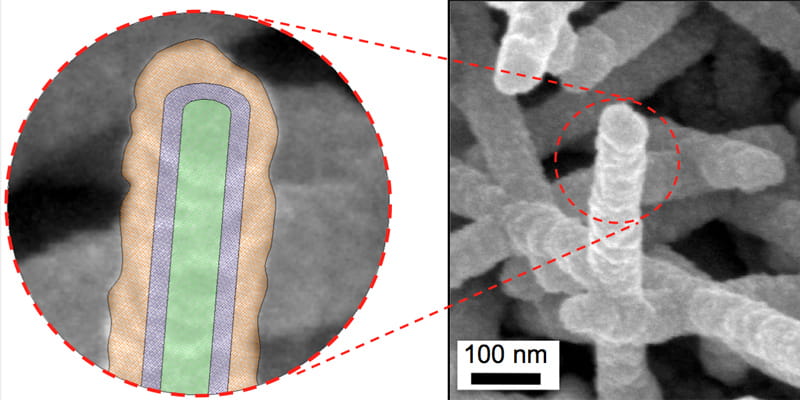
To make a test surface, McCarthy pours a solution containing billions of viruses onto his selected substrate. The rod-shaped viruses attach to the surface, forming a bristly layer of nanostructures. The tiny forest is then coated with a thin shell of metal that rigidly attaches the nanostructures.
Once coated, the viruses are rendered inert. What they’ve left behind is a coating of evenly spaced tendrils—“metallic grass,” as McCarthy calls it. This “grass” creates a capillary effect, which allows the coating to wick liquids across it and keep them in contact with the heat-transfer surface.
“This is quite an efficient technique for bio-templating nanostructures,” McCarthy said. “It requires no electricity, power, heat, or special equipment—just a series of solutions at room temperature. After the coating process is complete, the now-inert viruses are fully encased, resulting in a conformal coating of high surface area metallic nanostructures.”
Testing the Waters
With help from the viral framework, McCarthy’s lab can produce nanostructure-coated test surfaces of all shapes and sizes in a matter of hours. One “batch” of McCarthy’s Tobacco mosaic viruses can quickly coat a surface and turn it into a forest of tendrils that are perfect for wicking water.
“The nanostructures we build using the TMV act to stabilize the boiling process at large heat transfer rates,” McCarthy said. “These coating essentially act like a sponge, when a vapor bubble forms on the surface they wick liquid underneath it using capillary forces to delay the dry-out phenomena associated with critical heat flux. The result is a greater than three-times increase in the critical heat flux, which allows safe operation at higher and higher heat transfer rates.”
As part of his National Science Foundation CAREER award research, McCarthy’s team will look at the performance of dozens of different surface configurations with variations that range from the spacing of the nanostructures, to the overall shape and the metallic coating.
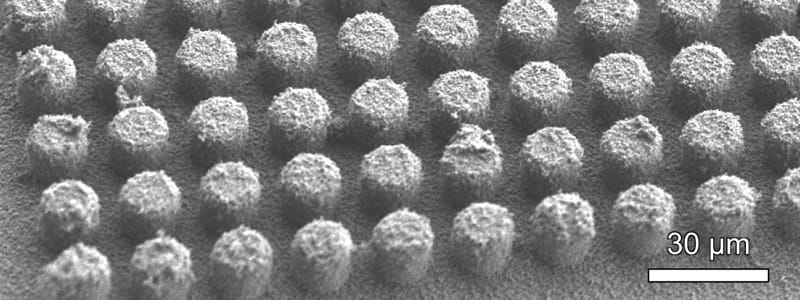
“Our lab has the unique ability to quickly design and build structured surfaces, thanks to our TMV technique,” McCarthy said. “We can also create surfaces that are extremely difficult, if not impossible, to do using other methods such as conformally coating complex microstructured surfaces and depositing nanostructures on low temperature materials. Because we can do this cheaply and relatively quickly, we can test numerous surfaces and make scientific conclusions based on large data sets.”
Preliminary results are already quite promising. The super-wicking surfaces have shown a 240-percent increase in critical heat flux, which means the maximum heat transfer rate achievable before critical heat flux occurs is more than three times as high as it was using the uncoated boiling surface.
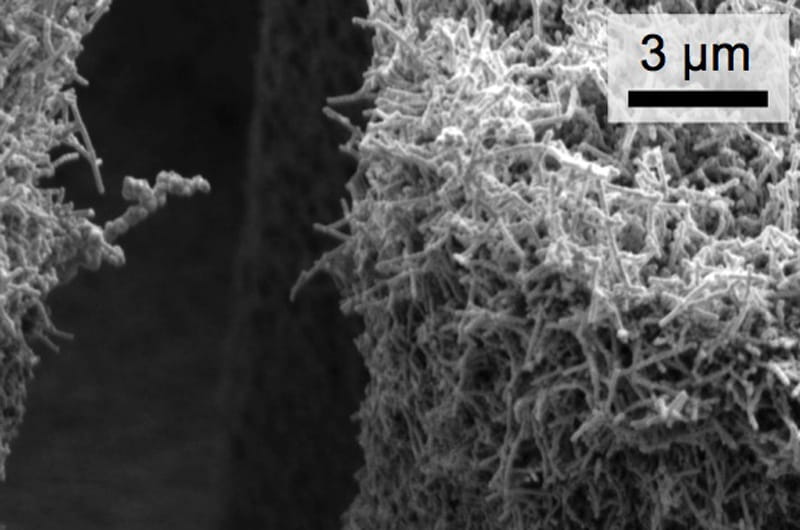
The “metallic grass” coating also results in a tripling of the efficiency of the boiling process. So if two pots of water—one with a nanostructure coating and one without—were heated to the same temperature, the pot coated with nanostructures would produce twice as much water vapor as the uncoated pot.
“In addition to studying the fundamentals of boiling heat transfer and its enhancement, this technology could be applied to new heat exchanger designs and high-performance thermal management systems of the future,” McCarthy said. “It could also be used to retrofit existing systems with self-assembled viral nanostructures—which could prove to be a cost-effective way to improve their efficiency.”
And, as McCarthy notes, a little improvement to the efficiency of something that’s widely used goes a long way.
In This Article
Contact
Drexel News is produced by
University Marketing and Communications.