It's estimated that 9.2 million American homes are served by lead water lines that have been poisoning water for decades. Research from Drexel and Seaflower Consulting, suggests that sound waves could be used to identify the lead lines without having to excavate and test each pipe.
As any percussionist or fidgety pen-tapper can tell you, different materials make different noises when you hit them. Researchers at Drexel University hope this foundational acoustic phenomenon could be the key to the speedy removal of lead water lines that have been poisoning water supplies throughout the country for decades. A recent study conducted with geotechnical engineering consultant Seaflower Consulting Services, showed that it is possible to discern the composition of a buried pipe by striking an accessible portion of it and monitoring the sound waves that reach the surface. This method could guide water utility companies before they break ground to remove lead service lines.
In the aftermath of the 2014 water crisis in Flint, Michigan, many utility companies have been diligently working to verify the materials of their service lines. These efforts have become increasingly urgent in the last two years due to the Biden Administration’s Bipartisan Infrastructure Act and the Environmental Protection Agency’s Lead Service Line Replacement Accelerators initiative mandating the removal of all lead pipes, serving an estimated 9.2 million American households — putting utilities on the clock to finish the job by 2033.
“Lead pipes are clearly an urgent public health problem and replacing them is rightly a priority, particularly in urban areas,” said Ivan Bartoli, PhD, one of the leaders of the team and a professor in Drexel’s College of Engineering. “But the challenge in these areas is that many of the lines are so old that records may not exist and utility companies are left to verify whether or not they’re made of lead before they begin the costly and lengthy process of digging them up and replacing them.”
Other noninvasive options include water sampling, which doesn’t identify the source of contamination and may miss lead lines; and closed-circuit camera inspection, which is difficult to deploy from outside and is not as effective when used in old pipes due to corrosion and scale buildup.
The current standard for testing pipes — entering homes to directly test the service line, or alternatively, excavating the line to obtain the sample — can be inconvenient for homeowners, disruptive for citizens and costly for utility companies. And the time it takes to verify pipes this way makes it unlikely that urban areas will be lead-free on the EPA’s timeline.
In Philadelphia alone, the Water Department estimates that some 20,000 of the 511,000 properties in the city may have lead service lines. Since 2017, the department has only been able to replace 2,600 of them, so finding a faster and less-destructive way to pinpoint which lines are lead could be crucial for meeting the EPA’s deadline without digging up most of the city’s streets and sidewalks.
The Drexel team’s approach is based on monitoring ultrasonic stress wave propagation, a technique frequently used for checking the structural health of pipelines, railroads and aircraft wings. But rather than simply showing that different types of pipes produce discernably unique acoustic stress waves when struck, in their study, recently published in the Journal of Nondestructive Evaluation, the team took the extra step of showing that those waves can be detected at surface level and their propagation translated into a signature for each type of pipe.
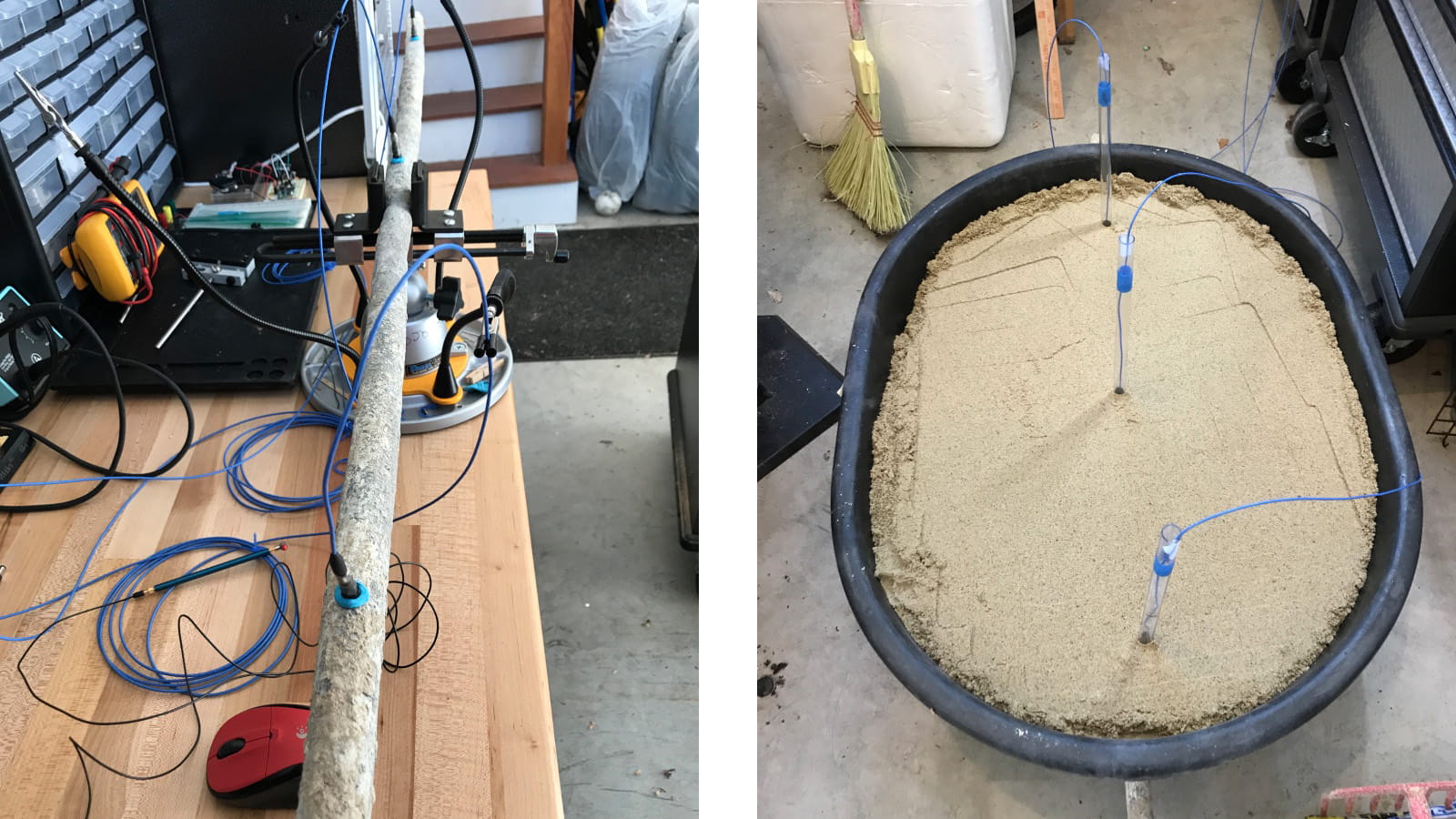
“Since wave speed varies with material type, the first arrival time of the wave on top of the surface differs for different service line materials,” they wrote. “For instance, for lead, guided waves along the pipe are slower since lead bulk wave speeds are much lower than speeds of other service line materials.”
The team experimented in the lab with lead, copper, steel and polyvinyl chloride (PVC) pipes, using piezoelectric accelerometer sensors to record stress wave propagation through each when struck with an instrumentation hammer. They repeated the process after partially filling each pipe with water and again after burying it in 30 centimeters of sand.
With the data collected, the team produced models — called dispersion curves — showing how quickly the waves reached each sensor and how their speed changed over time for each type of pipe and in each setting. The team believes these models could be used to identify pipes in the field.
“These results present a promising opportunity for noninvasive identification of service lines,” said Charles Haas, PhD, LD Betz professor of environmental engineering in the College of Engineering and one of the project leaders. “Additional testing will be necessary to verify this approach and to collect data on how waves propagate through different types of soils and those that are not homogenous, but this is an important step toward a solution to a very big problem.”
The release of $15 billion in funding from the Bipartisan Infrastructure Act for lead pipe removal in urban areas, rural communities and schools and childcare facilities is putting additional pressure on utility companies to come up with a viable technology to speed the identification and removal process.
The team is in the process of designing and testing a prototype of a system that could be used for pipe identification in the field by placing sensors on the ground between the water main and the house and using a probe and hammer to strike the curb stop valve of the service line to induce the acoustic waves. They have partnered with several water utility companies to test the prototype and begin to collect data to refine their models.
“Utilities need to work quickly to map and verify their service lines, but they also must ensure that there are no misses,” said Kurt Sjoblom, PhD, a former professor in Drexel’s College of Engineering, who is the founder of Seaflower Consulting Services and a leader of the project. “If excavating their entire water system just isn’t feasible – a tool like this could help point them in the right direction and cut down on unnecessary excavation.”
This research was supported by the Coulter-Drexel Translational Research Partnership.
In addition to Sjoblom, Haas and Bartoli, Fatmah Hasan and K.I.M. Iqbal, graduate students in the College of Engineering, contributed to this research.