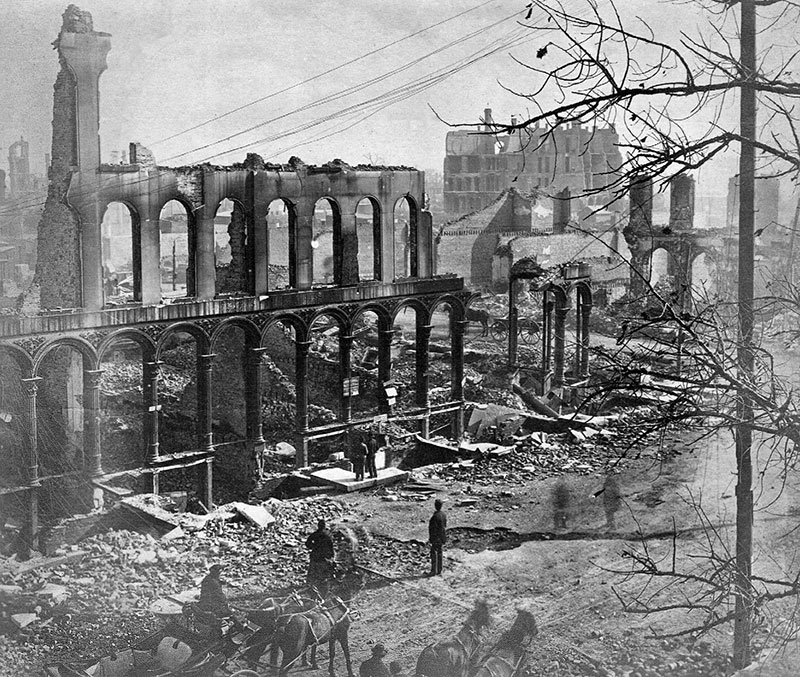
Safety concerns following the Great Chicago Fire of 1871 led to building safety codes that limited the use of wood in construction.
While it was one of the first and most common materials used to make things, when it comes to buildings larger than a log cabin, wood has been on the outs for more than a century. Due in part to an aversion from using it on safety grounds, following the Great Chicago Fire of 1871, and because of the superior strength and relative inexpensiveness of steel following the Industrial Revolution, wood has been relegated to a part-time role in smaller residential construction in the United States.
But that could all be changing in light of recent code changes related to the use of wooden building materials in larger buildings. A series of revisions to the International Building Code advise that wood, including a new fortified wooden building material called “mass timber,” can safely be used as the primary support structure in buildings as tall as 18 stories.
A recent New York Times story about the code update suggests that it will trigger a wave of wood construction driven by a demand for greener buildings with smaller carbon footprints — despite a higher cost for materials.
Drexel College of Engineering Professor Abi Aghayere,PhD, who co-authored a definitive text on wood construction in 2017, suggests that momentum has steadily been building for a return to the classic building material. However, building with wood today will likely look very little like it did in its heyday. He recently shed some light on why the changes are happening now and what they’ll mean for building construction.
When we talk about “building with wood” what does this actually mean? Isn’t wood already used to frame out houses and buildings? What is the difference between that and structural wood construction?
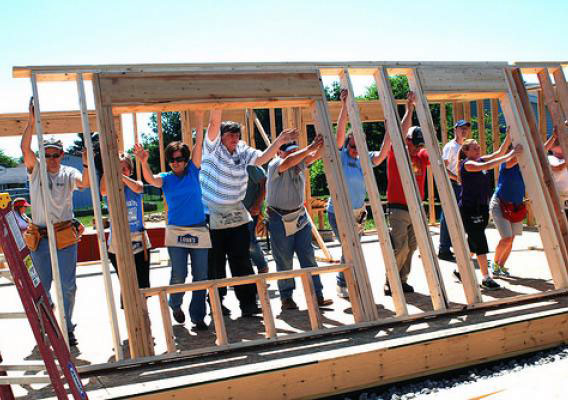
Light-wood framing is used in single-family dwellings and some strip malls, but structural wood construction has waned in the United States until recently.
Yes, we already build single-family dwellings and even strip malls with wood — sawn lumber or light-frame construction. This construction is in a different category of the International Building Code than what would be considered “heavy timber” buildings.
The code prescribes the allowable maximum height and maximum floor area of buildings based on the type of construction, the fire resistance capabilities or fire rating, and the occupancy or use of the building. So, aside from that used in single-family residential projects, most wood that is currently being used in construction is only on the interior of buildings or in smaller projects that are not many stories high. Or for just a few floors of a hybrid project that also uses steel and concrete as the base or podium structure.
When we talk about building larger buildings with wood, this is achieved using “heavy timber” or “mass timber” construction where the wood is providing the main structure of the building. Heavy timber construction has been around for a long time. One of the big advantages in addition to being able to build taller buildings is that you can expose the heavy timber, as can be seen in the beautiful timber arches in some churches.
Why has wood construction been out of favor for so long?
This is primarily because of the fire-safety issues with light-frame construction and the limited axial load carrying capacity of light-frame wood members. Sawn lumber, because of its small size, possesses very limited fire-resistance capabilities. So, to protect it from fire, all sides of the lumber are typically enclosed in a finish material that is fire-resistant, such as gypsum wall board. Whereas other materials, like concrete, are naturally fire-resistant so there is no need for another fire-proofing step during construction of concrete buildings.
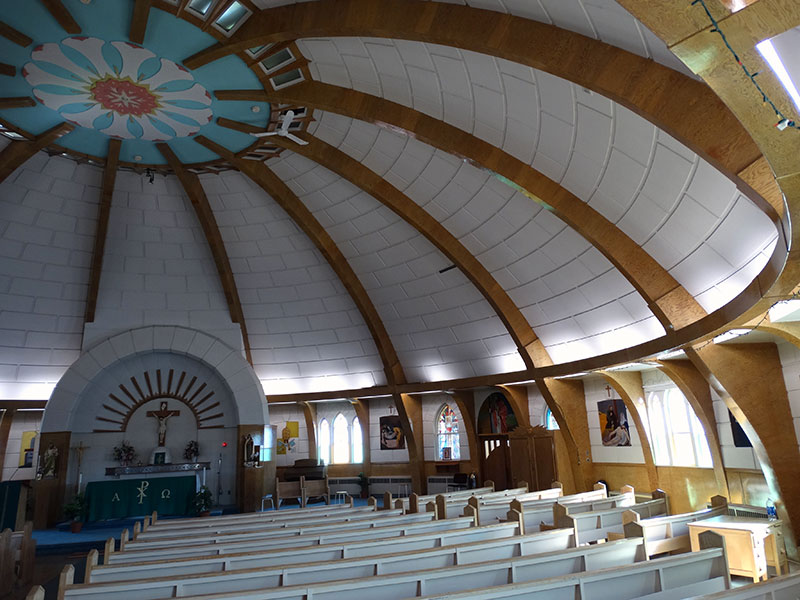
While heavy timber construction was often used in large buildings like churches, fire safety concerns, combined with the rising cost of large beams and scarcity of old-growth trees has diminished its popularity in the United States.
Heavy timber has some resiliency to fire as the large members form a char layer on the outside that insulates the inner parts of the wood member preventing them from being consumed. But there is still a safety concern, because charred members cannot sustain as much of a load — thus the International Building Code limited heavy timber construction to six stories. So as the demand for taller buildings increased, construction with heavy timber became less common because of competition from other building materials like steel and concrete.
It’s also worth noting that heavy timber can be comparatively very expensive as a construction material because of the growing scarcity of old-growth trees big enough to produce the massive beams needed for this type of construction.
What are the main developments in wood construction materials that are now allowing for more use of heavy timber in taller buildings?
The biggest development in heavy timber construction is “mass timber” or, to be specific, a product called cross-laminated timber (CLT), which has allowed wood to be used for taller buildings because it is very effective in resisting fire in comparison to standard lumber. CLT consists of stacked layers of typically low-grade wood, glued together to form a solid material, with adjacent layers oriented perpendicular to each other. A 3-ply CLT has three layers and a 5-ply CLT has 5 layers. CLT has a substantial load-bearing capacity when used in wall panels and floor slabs and it shrinks less than sawn wood used in light-frame construction.
It was developed in Germany and Austria and has been used in Europe since the 1990s. It has already been used successfully in Europe and Canada for tall buildings as high as 14-18 stories.
What are the advantages of building with wood?
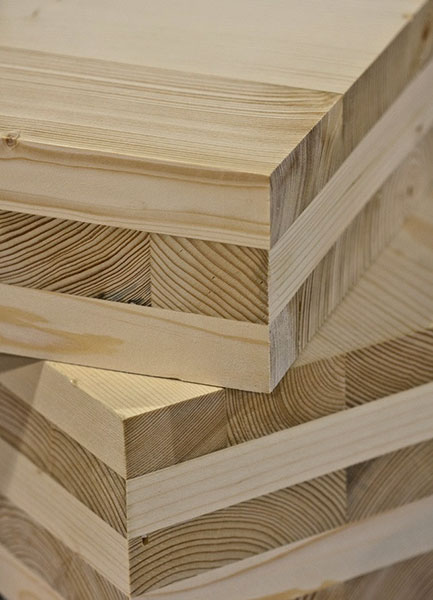
A building product called cross-laminated timber has created a surge in mass timber construction in Europe and Canada over the last two decades and the latest revisions to the International Building Code have paved the way for wider adoption in the U.S.
One of the advantages of CLT over sawn lumber is that it does not lose its strength during a fire. CLT develops a char layer on the outside that protects the inner portions of the load-bearing CLT wood member.
It is also more resilient in a wider range of environments because it does not experience the same magnitude of shrinkage that sawn lumber does. In tall buildings, CLT is being used for both the floor and roof slabs, and the wall panels; the CLT wall panels support the gravity loads from the floors and roof slabs. They are also strong enough to be used to resist the lateral or horizontal forces from wind and earthquakes.
The fact that wood structures also have a comparatively smaller carbon footprint compared to concrete or steel structures is a benefit that could have been a factor in the ICC’s consideration. Some estimates put the carbon footprint of a typical wood building at approximately 25 to 40 percent of the carbon footprint of steel or concrete structures.
And since CLT is made from sawn lumber pieces, which do not necessarily have to be of the highest quality or highest stress grade, using it doesn’t drive up the demand for old-growth (large) timber. There has been some research on using low grade sawn lumber for CLT members. So CLT might allow for the use of a wider variety of wood species and stress grades.
What will CLT buildings look like?
Even with the code revisions we aren’t likely to see buildings that are entirely wood, because it takes a mix of materials to make them resilient to a variety of environmental stresses.
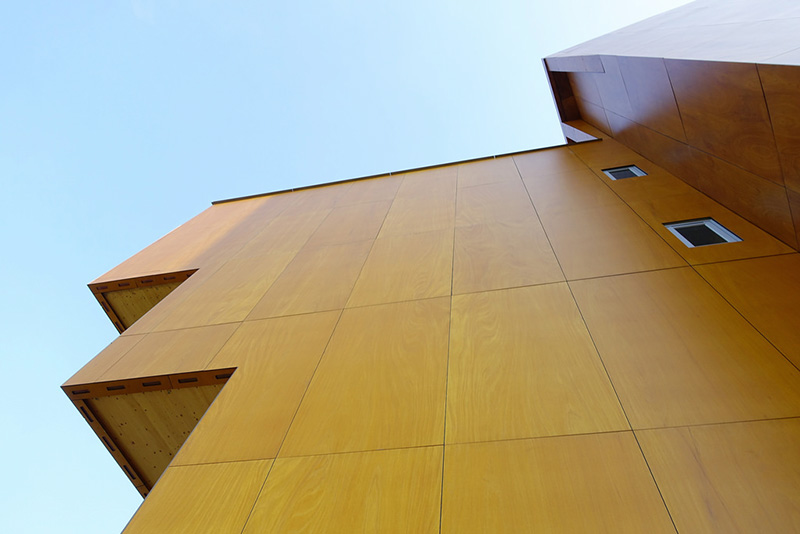
Cross-laminated timber is enabling the construction of taller wooden buildings.
For example, the tallest wood CLT building in the world is currently the 18-story University of British Columbia’s Brock Commons Building. This is a 17-story CLT structure built on top of a one-story concrete podium structure and it uses 5-ply CLT floor panels supported on glulam columns and two concrete core walls which also act as the earthquake- and wind-resisting system. The ground and second floors are of concrete construction and the roof is steel-framed, while the remaining 16 floors are of CLT construction.
The construction of the building was started in June 2016 and the entire structure for the 18-story building was completed in August 2016 – a record time of just over 2 months, with the interior construction and finishes completed by fall of 2017.
What do you see as the main challenges for wider adoption of wood construction?
There are a number of challenges for wider adoption of wood for tall buildings.
We are still understanding how the connections of wood members in a high-rise building will respond during service and during a fire event.
The higher the building, the larger the axial load on the wall panels at the lower levels. The potential for crushing of the wood in the CLT floor panels is high since wood is weaker in compression perpendicular to its grain direction. Research is suggesting that a hybrid connection, that includes concrete, would make for a stronger connection and could actually allow for CLT high-rise buildings of up to 50 stories.
Other questions concern the water damage of a sprinklered tall wood building after a fire or water damage from fire-fighting operations. Will mold become an issue with the sustained wetting of the wood? Will the wood building and the property inside be salvageable after a fire or will it have to burn out completely?
The way wood responds in different climates could also be a limiting factor. Wood has a tendency to shrink in dry weather. Though CLT wood members are much less susceptible to shrinkage compared to sawn lumber, the amount of shrinkage in tall CLT buildings could still be appreciable for very tall buildings. Also, CLT is susceptible to creep – that is, the continuous deformation of a CLT member over time under constant load.
In addition, there might be liability insurance concerns. How will the liability insurance for CLT tall buildings compare to typical concrete and steel buildings? Will some insurance companies simply shy away from insuring tall wood buildings — leading to higher insurance rates?
And there is always a certain amount of skepticism and hesitance to accept new building systems in general. The concept of using wood for tall buildings is still quite new in the United States so it will likely take more testing and use before it fully catches on.
Where do you think mass timber construction is most likely to catch on?
The use of wood for taller buildings appears to be catching on faster in the areas of the country with a thriving forestry industry. Oregon and Washington appear to be leading the way in the United States in the use of CLT, while British Columbia appears to be leading the way in Canada.
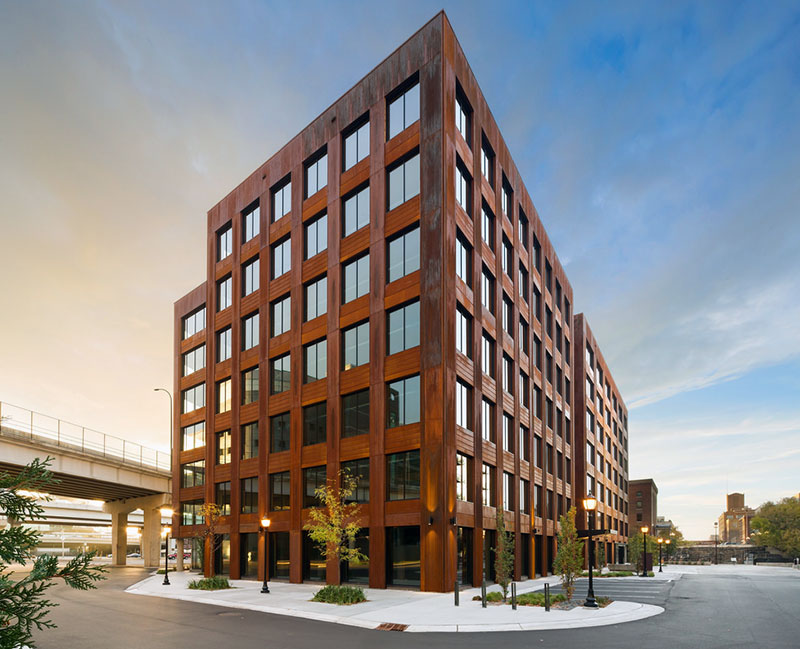
Mass timber construction is already gaining momentum in the Pacific Northwest and Midwest.
Since CLT is prefabricated, the construction time of typical CLT buildings is much shorter than comparable steel or concrete buildings; also because the weight of CLT buildings is lower than a comparable steel or concrete building, the foundation costs of CLT buildings are lower, and the seismic lateral forces induced on the building are also much lower; as a result, some developers, architects, engineers and owners, with an eye on the potential cost savings, may turn to CLT as their preferred material for high-rise buildings, especially in urban areas.
Also, whether tall wood buildings are allowed locally will depend on if the local building code adopts the IBC requirements without modification. The acceptance of tall wood buildings may vary from jurisdiction to jurisdiction.
Abi Aghayere, PhD, is a professor of civil engineering in Drexel’s College of Engineering. His text on wood construction, “Structural Wood Design,” is in its second edition from CRC Press.