At some point in the near future, a shirt will no longer be just a shirt. Your average Eagles jersey will eventually be able to call your mother, take your temperature, and serve as an electromagnetic shield. Then, the advances enabling such technology will be traced back to the painstaking steps taken by materials scientists all over the world, like Simge Uzun, a doctoral candidate in the College of Engineering Department of Materials Science and Engineering (MSE).
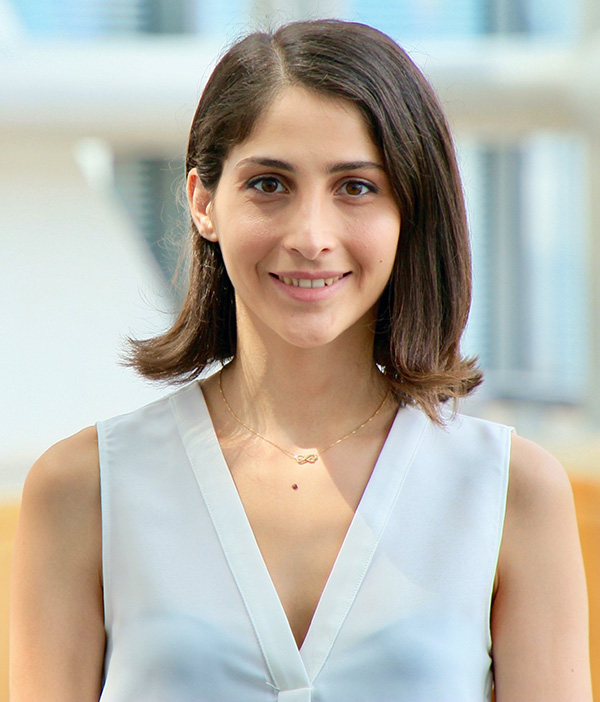
Simge Uzun
Uzun is researching how to transform natural and synthetic yarns into highly conductive yarns, converting simple, everyday items into an application of technology at its most personal: not just for phones or laptops or SMART cars, but for the actual clothes we put on our bodies.
She uses, of course, the carbon-based, two-dimensional layered materials called MXenes developed at Drexel in 2011. Since their discovery, MXenes have proven so versatile and conductive that a multitude of applications—from antennas to electromagnetic shields to medical devices—are being explored here and abroad. Wearable technology is among these.
When Uzun arrived at Drexel two years ago to pursue her PhD, she already had a background in fiber science gained at Cornell University and in textile engineering gained at Istanbul Technical University, one of Turkey’s best engineering schools. Researchers at the A.J. Drexel Nanomaterials Institute introduced her to the process of synthesizing the nanometer-thin sheets of MXene for functional fabrics, and she took it from there.
“A great example of a wearable smart textile application is a heated jacket. That’s great for you in the winter, right? But now, you’d have an external battery. You have to carry it. It’s bulky. It’s unwieldy. And if you throw it in the dryer, you could have an explosion,” said Uzun. “So we are working towards getting rid of the battery and engineering MXene-based fibers and yarns that have the capacity to store energy as well as those external batteries. Then, we can just knit or weave these functional yarns seamlessly into your clothing.”
Uzun’s research is co-advised by Dr. Yury Gogotsi, the Charles T. and Ruth M. Bach Distinguished University Professor in MSE and director of the A.J. Drexel Nanomaterials Institute; and Associate Professor Genevieve Dion, Westphal College of Media Arts & Design, and director of Drexel’s Center for Functional Fabrics.
“Simge brought her textile background to my materials science lab,” said Gogotsi. “Her work on MXene-enhanced textiles may lead to a real breakthrough in wearable technology.”
In concert with Gogotsi and Dion, Uzun has filed a disclosure for the work under the title “MXene Coated Yarns and Textiles for Functional Fabric Devices.” The study is submitted and is currently under revision.
All stitched up
In the recent past, researchers have worked to demonstrate the performance of textiles enhanced with highly conductive materials. Generally, however, they stopped there, not advancing past that stage to show that the conductive yarns are scalable and processable for manufacturing. It was the industrial-size knitting machines at Drexel’s Center for Functional Fabrics that matched Uzun’s research ambitions with the capacity to see them through. One of the earliest baseline challenges was finding the right parameters for knitting MXene-coated yarns into textile-based devices that were durable and flexible enough to withstand wear and washing.
“Simge brought her textile background to my materials science lab. Her work on MXene-enhanced textiles may lead to a real breakthrough in wearable technology.”
Yury Gogotsi
The most commonly used pattern in knitted garments is the so-called single jersey knit, which comprises a series of loops formed in close proximity to form a swatch of fabric. However, once coated with MXene the yarns tended to lose their inherent flexibility; among other issues, the closeness of each loop to its neighbor caused friction that led to material breakdown. So Uzun, using advanced manufacturing knitting machines at the Center, experimented with a variety of patterns—interlock, single jersey, and half-gauge—until she found a combination that produced coated yarns with a bit more space between the loops, overcoming the problem of friction.
The next step was washing the yarns: would that process reduce conductivity or otherwise introduce breakdown in the coating? In order to test the durability of the materials, Uzun washed the coated yarns for 45 cycles at temperatures ranging from 30° C to 80° C, much higher temperatures than your average wash cycle.
The results were promising. The yarns sustained their conductivity under harsh environments. The resistance of the yarns remained stable. And the MXene loading held.
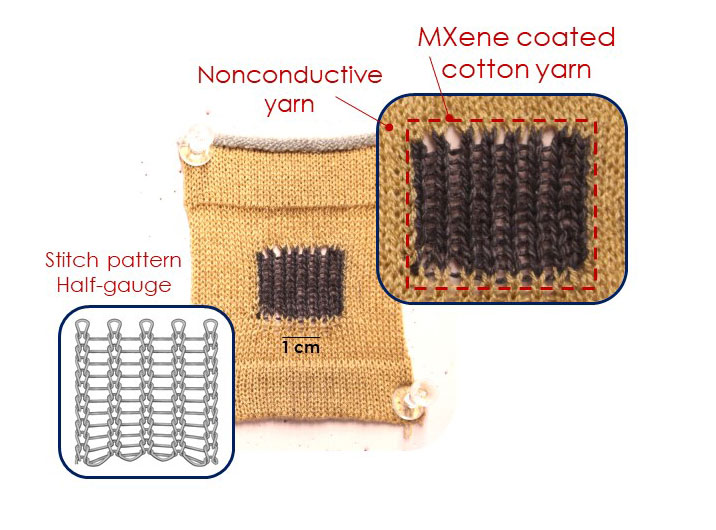
This image shows the highly conductive MXene-coated cotton yarn (black) knitted into a regular swatch of nonconductive commercial yarn on industrial-size knitting machines at Drexel’s Center for Functional Fabrics, using a half-gauge stitch pattern.
“We can easily scale the production of MXene-based conductive yarns because we use a simple dip-coating approach to coat the yarns,” said Uzun. “People use this approach in the textile industry. It’s almost like yarn dyeing—we adopted the properties of traditional dyeing to our own process. Here’s the key part: since MXenes are two-dimensional flakes, we can actually tune the size of the flakes we’re using. I was able to get very high MXene loading because the first coating process started with using smaller flakes that can penetrate into the fibers.
“Once we saturate the fiber level,” she added, “then I start using the larger flakes to coat the yarn surface. It’s a two-step loading process.”
The amount of material load depends on the application. For use with sensors, for example, the conductivity requirements are not high: to register certain diagnostics like heart rate or temperature through touch, 30-to-40% weight of MXene on the yarn is sufficient, said Uzun. For use with energy storage, the percentage is closer to 80%.
A range of applications
Now that Uzun has proven that MXene-based yarns and textiles can be engineered for conductivity and then scaled, the range of applications for these yarns is, by all accounts, unlimited, from briefcases that provide electromagnetic shielding for laptops and for the humans who use them, to shirt pockets that can be reinforced to shield credit card information from electronic pickpockets, to textile supercapacitors that replace bulky batteries.
“It’s actually very exciting to me that so many companies are involved with functional textiles,” said Uzun. “Since we demonstrated the knittability and washability of the produced yarns, now the possible applications for these yarns including electromagnetic shielding and heated fabrics—gloves, jackets—are endless,” said Uzun.
“I love working on these materials,” she added. “It really enables me to learn a lot about fundamental materials science, but also to be able to see the end application. I have an opportunity to finish what I started. These materials are not just part of a research paper; there is a potential for them to make it to market. We are working towards enabling that.”